Custom home construction is a journey that transforms your vision into a tangible living space. Pre-Engineered Buildings (PEBs) have revolutionized this process, offering a streamlined and efficient path to creating your dream home.
What Is A Custom Home Design?
A custom home design is a unique architectural plan tailored to the specific desires and lifestyle of the homeowner. Unlike standard designs, a custom home is conceived from scratch, allowing for personalized layouts, materials, and features that reflect the owner’s preferences and needs.
Are Custom Builds Expensive?
In the Philippine context, custom home construction costs can be considered expensive due to the personalized nature of the design and construction process. The cost of building a custom home in the Philippines can vary significantly based on several factors, including location, materials, design complexity, and level of customization.
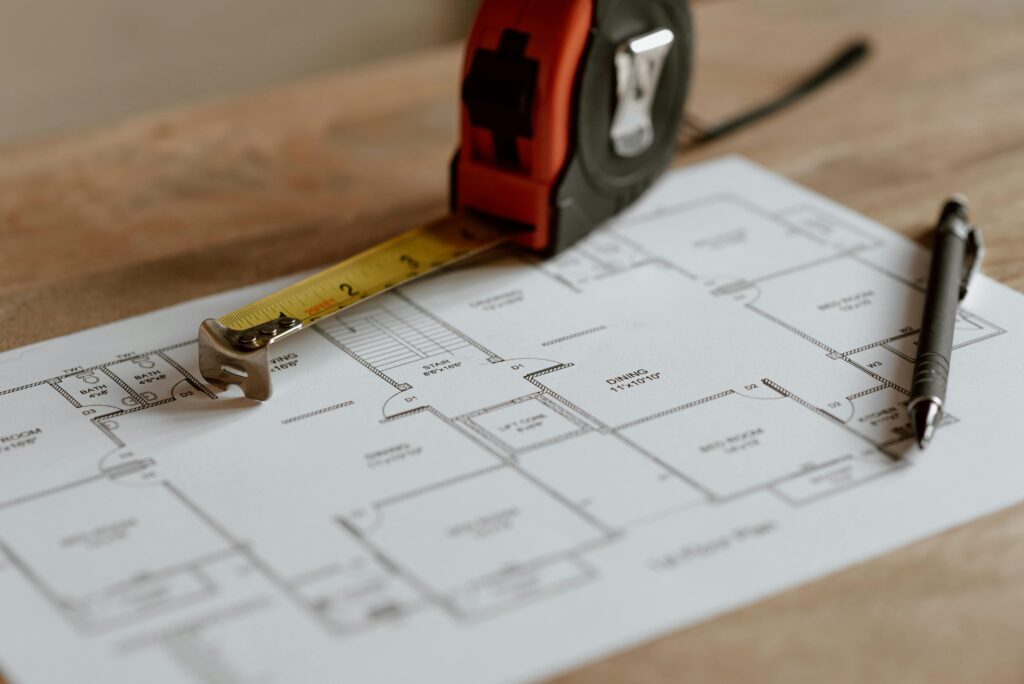
According to ARCGO, the average cost to build a house in the Philippines in 2023 ranges from approximately PHP 23,000 to PHP 35,000 per square meter. For custom-built homes, the costs can be anywhere from PHP 28,000 to PHP 50,000 or more per square meter, depending on the design, materials, and level of customization involved. These figures indicate that custom homes can be more expensive than standard builds, especially when premium materials, advanced features, and innovative designs are desired.
While custom builds offer the advantage of personalization and can result in a home that perfectly suits the homeowner’s needs, they do come with a higher price tag in the Philippines. Prospective homeowners should prepare for these costs and work closely with architects and engineers to ensure that their vision aligns with their budget.
Rise Of PEBs In The Construction Industry
PEBs have surged in popularity due to their adaptability, efficiency, and cost-effectiveness. These structures are designed and partially assembled in a factory setting before being shipped to the construction site for final assembly, significantly reducing construction time and labor costs.
Benefits Of Using PEBs (Pre-Engineered Buildings) In Custom Home Construction
a. Versatile
PEBs offer a high degree of design flexibility, allowing for a range of architectural styles and customizations. This versatility ensures that each PEB custom home can be as unique as its owner’s vision.
b. Cost-Effective
The streamlined manufacturing and construction process of PEBs leads to significant cost savings. With components pre-engineered to fit together seamlessly, there is less waste and reduced labor costs, making PEBs a budget-friendly option.
c. Reduced Construction Time
The prefabrication of PEB components off-site means that the construction timeline is significantly shorter compared to traditional building methods. This efficiency allows homeowners to move into their new custom homes much faster.
d. Durable
PEBs are engineered to meet strict building codes and withstand various environmental stresses, ensuring long-term durability and safety for the occupants.
e. Environmentally Sustainable
PEBs are often made from recyclable materials and designed to be energy-efficient, contributing to a smaller environmental footprint. The precision of pre-engineering also minimizes waste during construction.
How To Create A Custom Home Made Of PEBs
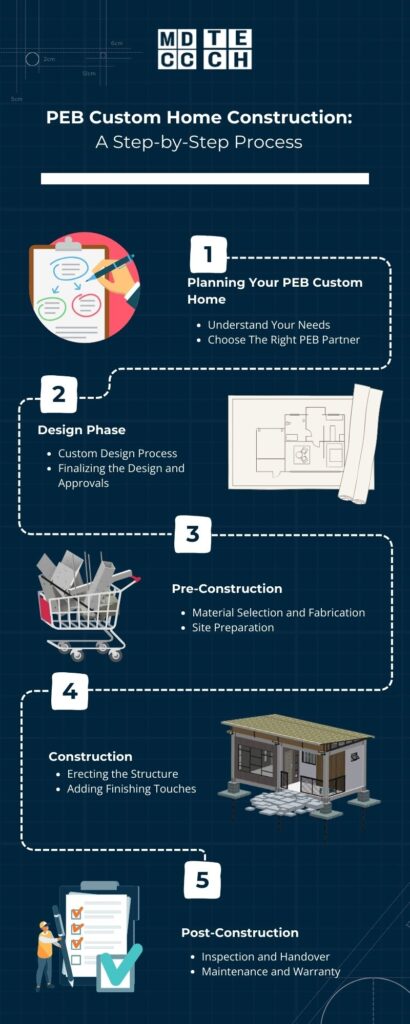
Phase 1: Planning Your PEB Custom Home
Understand Your Needs
When planning a custom home, it’s crucial to have clarity on your requirements, budget, and design preferences. A detailed budget is essential to avoid unexpected costs and keep the project on track. Understanding your needs helps in making informed decisions about the design, materials, and features you want in your home, ensuring that the result aligns with your lifestyle and preferences.
Choose The Right PEB Partner
Selecting the right custom home builders experienced in PEB homes is vital. Look for technical competency, quality of materials used, skilled and experienced teams, and the ability to stick to deadlines. MDCC TECH, with its expertise in PEB structural legacy parts and custom homes, can be a valuable partner in this process.
MDCC TECH offers Pre-Engineered Building (PEB) structure components that are smartly designed for efficiency in construction. These parts are cost-effective, easy to assemble, flexible, durable, and energy-efficient, making them the best material for customizing your home.
Phase 2: Design Phase
Custom Design Process
PEB custom home construction firms collaborate with clients to create a custom home, involving architects, engineers, and the homeowner in the design phase. This collaboration is crucial to ensure that the home meets the owner’s vision while also being structurally sound and efficient.
Finalizing the Design and Approvals
The design is finalized through 3D modeling and simulations, which help in visualizing the final product. Obtaining necessary permits and approvals is also a critical step in this phase to ensure that the construction complies with local regulations and standards.
Phase 3: Pre-Construction
Material Selection and Fabrication
Materials for PEB components are selected based on the custom design, including beams, columns, and diagonal bracings. These components are then fabricated in a controlled factory environment, often using materials like Glass Fiber Reinforced Polymer (GFRP) and Fiber Metal Laminate (FML), which are known for their strength and durability.
Site Preparation
While components are being fabricated, the construction site must be prepared. This includes clearing the land, excavation, and laying the foundation, which are essential steps to ensure a smooth construction process.
Phase 4: Construction
Erecting the Structure
The PEB components are assembled on-site in a step-by-step process. Skilled labor and technology play a significant role in ensuring that the assembly is done accurately and efficiently.
Adding Finishing Touches
After the structure is erected, systems such as electrical, plumbing, and HVAC are installed. Exterior and interior finishes are then applied to complete the custom home according to the homeowner’s specifications.
Phase 5: Post-Construction
Inspection and Handover
The completed home undergoes an inspection to ensure it meets all regulations and standards. The final handover includes walkthroughs and documentation to ensure that the homeowner is satisfied with the final product.
Maintenance and Warranty
PEB custom homes require maintenance to ensure their longevity. Construction companies typically offer warranty options to cover any defects or issues that may arise after construction.
The Bottom Line
Considering the benefits of Pre-Engineered Buildings (PEBs) for custom home construction in the Philippines can be a game-changer. With their versatility, cost-effectiveness, and reduced construction time, PEBs offer an efficient solution to turn your dream home vision into reality.
By partnering with reputable PEB builders like MDCC TECH, prospective homeowners can navigate the custom home construction process with confidence, ensuring a personalized, durable, and environmentally sustainable living space that aligns with both their aspirations and budget. Embrace the innovation of PEBs and transform your custom home construction journey into a streamlined and satisfying experience.
Start planning your PEB custom home construction project now! Contact us today for more information on how we can help you build your dream home.
You can also reach us at 0917-627-3492 or follow and send us a message on Facebook or LinkedIn.