Pre-engineered buildings (PEB) have revolutionized the construction industry by offering a system that significantly reduces construction time and cost while providing flexibility in design and long-term durability.
Understanding what is PEB structure, their components, benefits, and applications provides a solid foundation for your next construction project. This guide aims to equip you with everything you need to know about PEB structures, highlighting why they are an optimal solution for modern construction needs.
What Is PEB Structure?
Pre-engineered buildings (PEBs) are structures that consist of factory-built components designed to be easily assembled on-site. They are known for their high structural strength, economical design, and ability to supersede conventional fabrication methods. PEBs are lighter than traditional buildings by up to 30% and are tailored to meet client-specific requirements based on actual design calculations.
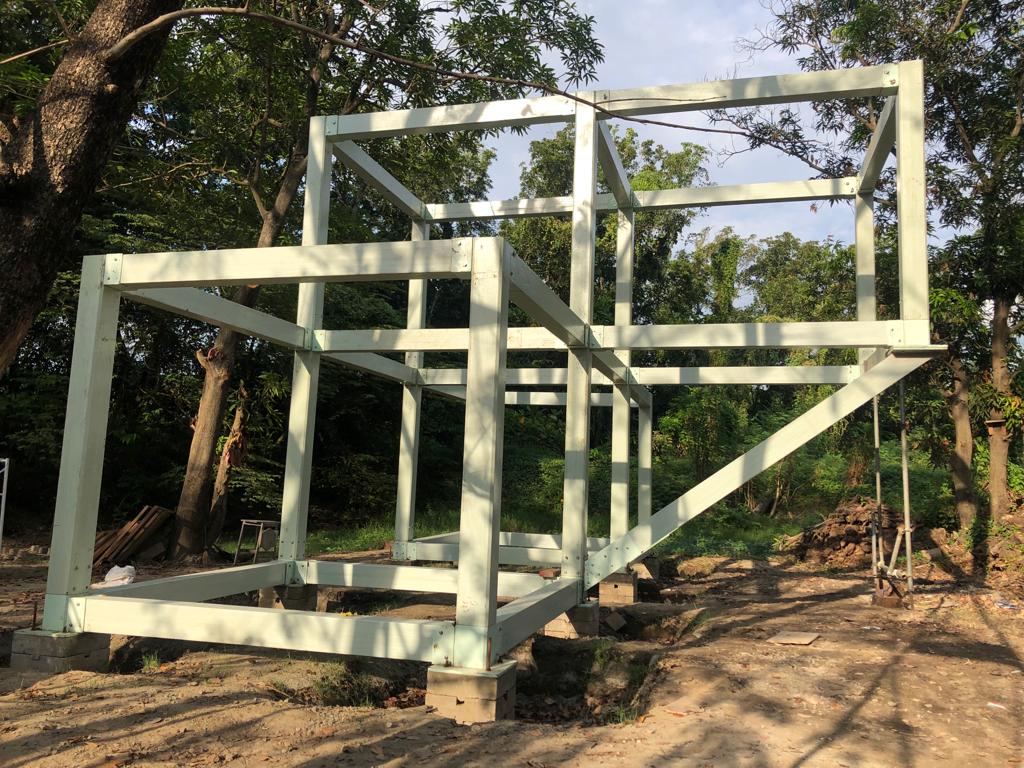
Key Components Of A PEB Structure
The components of a PEB structure are crucial as they determine the building’s strength, durability, and functionality. Here’s a brief overview of each key component:
Structural Framing System | |
Columns | Vertical supports that carry loads from the roof and floors |
Beams | Horizontal members that support loads from floors and roof |
Rafters | Sloped beams that support the roof structure |
Purlins | Horizontal beams providing support to the roof panels |
Girts | Horizontal beams providing support to wall panels |
Eave Struts | Horizontal framing members located at the eave of a building to support roof and wall panels |
Wind Bracing | Elements that provide resistance to lateral forces |
Diagonal Bracing | Components that stabilize the structure against lateral loads |
Cable Bracing | Cables used to provide additional support and stability |
Roofing and Wall Systems | |
Roof Panels | Protective layers on the roof that resist environmental loads |
Wall Panels | Protective layers on the walls that provide insulation and resistance to environmental loads |
Skylights and Wall Lights | Allow natural light to enter, enhancing energy efficiency |
Foundation Elements | |
Concrete Foundation | The base that supports the structure |
Anchor Bolts | Used to secure the structure to the foundation |
How PEB Structures Are Designed And Fabricated
The PEB construction process involves using CAD software to create detailed plans and 3D models. The design phase considers the building’s use, location, and safety standards. Fabrication occurs in a factory setting, where materials are cut, shaped, and welded. Quality control ensures each component meets specifications before being shipped for assembly.
Materials Used In Creating PEB Structure Components
Steel
The cornerstone of PEB, steel offers unmatched strength and versatility. Its high strength-to-weight ratio means less material delivers more structural integrity, making it cost-effective. Steel’s adaptability allows for pre-engineering into various shapes and sizes, tailored to specific PEB needs. Furthermore, it boasts excellent resistance to fire, moisture, and pests, contributing to its longevity and reducing maintenance costs.
Glass Fiber Reinforced Polymer (GFRP)
GFRP stands out for its exceptional lightweight properties, significantly reducing transport and assembly costs. Its corrosion resistance feature ensures longevity in harsh environmental conditions, while the high tensile strength provides structural stability. GFRP’s flexibility in design allows for innovative architectural shapes, making it a preferred choice for aesthetically driven projects.
Fiber Metal Laminate (FML)
FML is a hybrid material that combines the lightweight features of fiber with the strength of metal, offering an optimal strength-to-weight ratio. This material is particularly suited for environments requiring durability and resistance to fatigue and impact. Its excellent performance in demanding conditions makes it ideal for specialized PEB applications, offering cost savings through longevity and reduced maintenance.
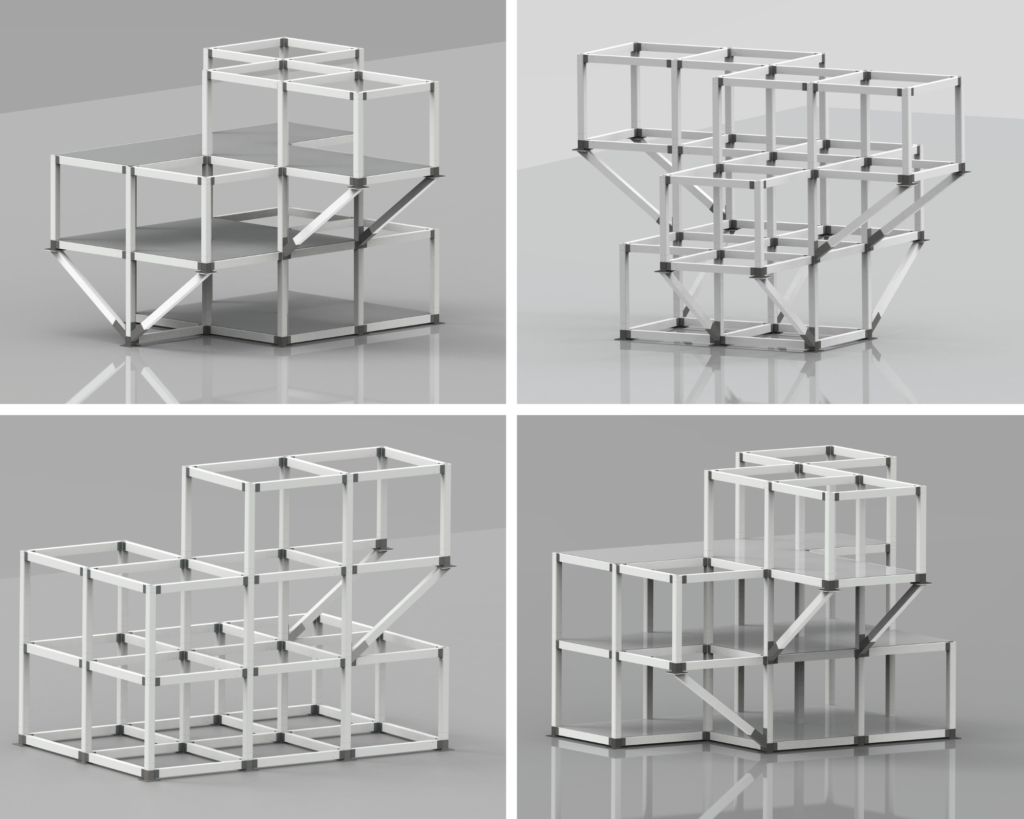
Advantages Of PEB Structures In The Construction Industry
Lightweight Structural Composition
PEBs use materials like Glass Fiber Reinforced Polymer (GFRP) and Fiber Metal Laminate (FML) that offer strength without weight, significantly reducing foundation requirements and enabling swift construction on varied terrains.
Accelerated Construction Timelines with Reduced Costs
Since PEB components are manufactured off-site, construction becomes like assembling a giant Lego set. This significantly reduces on-site construction time compared to traditional methods requiring brick-and-mortar work. Faster construction translates to reduced labor costs and earlier project completion, allowing you to start using the building sooner.
Improved Durability and Safety Features
PEB structures are inherently strong and are engineered to endure various weather conditions, including high winds, heavy snowfall, and even earthquakes (depending on the design). Additionally, the pre-engineered nature ensures the components meet specific load-bearing capacities, enhancing overall building safety.
Enhanced Design Flexibility
While PEBs might seem limited, there’s actually a good amount of design flexibility. You can choose from various pre-designed layouts and customize aspects like wall and roof panels, cladding materials, and even incorporate skylights or mezzanines for a more unique look.
Expandable and Portable
PEB structures can be modular, meaning they can be easily expanded by adding additional bays (sections) later on. PEBs distributed by MDCC TECH can even be disassembled and relocated to a new site, making them suitable for temporary or relocatable needs.
Low-Maintenance Cost
Steel, GFRP, and FML are low-maintenance materials compared to materials like concrete or wood. PEB structures generally require minimal upkeep, reducing long-term costs.
Energy-Efficient
PEBs can be designed to be energy-efficient in a couple of ways. The metal roof and wall panels can be insulated to minimize heat transfer, and skylights can be incorporated to utilize natural light, reducing reliance on artificial lighting.
Overall, PEB structures offer a compelling option for various construction projects due to their speed, cost-effectiveness, durability, and adaptability.
Applications Of PEB Structures
PEBs are versatile and can be used in various settings, including PEB building solutions for:
1. Residential Houses
While less common than traditional constructions, PEBs can be used for residential houses. Their modular nature allows for speedy construction of pre-designed modern homes. Also, PEBs offer a sustainable housing solution, customizable to various layouts and designs, ensuring energy efficiency through insulation and natural lighting.
2. Beach Houses
PEBs can be a good fit for beach houses due to their:
- Durability: GFRP and FML resist corrosion from salty air better than some traditional materials.
- Clear Spans: PEBs can provide large open spaces with minimal interior columns, offering unobstructed ocean views.
- Faster Construction: This is beneficial in beachfront locations where building permits or weather conditions can cause delays.
3. Offices
PEB designs facilitate adaptable office spaces that can evolve with business needs, ensuring a modern and efficient work environment. They offer:
- Speedy Construction: Ideal for quickly setting up temporary or branch offices.
- Expandable Design: PEBs can be easily expanded as your business grows.
- Open Floor Plans: The clear span allows for flexible office layouts.
4. Retail Spaces
PEBs allow for visually appealing retail environments, with vast open spaces and flexible layouts to enhance customer experiences. It can be used to construct retail stores, particularly large big-box stores. They provide:
- Large Open Floor Plans: Perfect for displaying merchandise and maximizing space utilization.
- High Ceilings: Can create a more spacious and airy feel for customers.
- Cost-Effectiveness: PEBs can be a budget-friendly option compared to traditional constructions for large retail spaces.
5. Warehouses
The strength and durability of PEB materials are ideal for creating large, open-plan warehouses, capable of supporting heavy loads and efficient logistics. Warehouses are one of the most common applications for PEBs due to their:
- Durability: PEB structures can withstand heavy loads from stored goods.
- Clear Spans: Provide large open storage areas without interior columns, maximizing storage capacity.
- Fast Construction: Allows for quick construction of warehouses to meet storage needs efficiently.
6. Factories
Engineered for industrial demands, PEBs accommodate heavy machinery and workflow efficiencies, ensuring safety and durability in demanding environments. Similar to warehouses, PEBs are a popular choice for factories because of:
- Large Clear Spans: Accommodate large machinery and production lines.
- Expandability: Factories can be easily expanded as production needs increase.
- Durability: Steel can withstand demanding industrial environments.
- Cost-Effectiveness: PEBs offer a faster and potentially more affordable way to build factories compared to traditional methods.
Final Thoughts
Pre-Engineered Buildings stand out as a modern, innovative solution for construction projects, offering a blend of strength, efficiency, and adaptability. Their design and fabrication leverage advanced materials and technology to provide a range of benefits that traditional construction methods struggle to match. Whether for residential, commercial, or industrial applications, PEBs present a compelling choice for those seeking to optimize their construction projects in terms of cost, time, and performance. As the construction industry continues to evolve, the role of PEBs is likely to expand, underscoring the importance of exploring PEB options for future construction needs.
Considering PEB for your project? MDCC TECH offers custom-designed PEB structures to perfectly suit your needs. Get in touch with us today to see how we can help you bring your vision to life!